CASE STUDY
Driving operational success through capital project execution
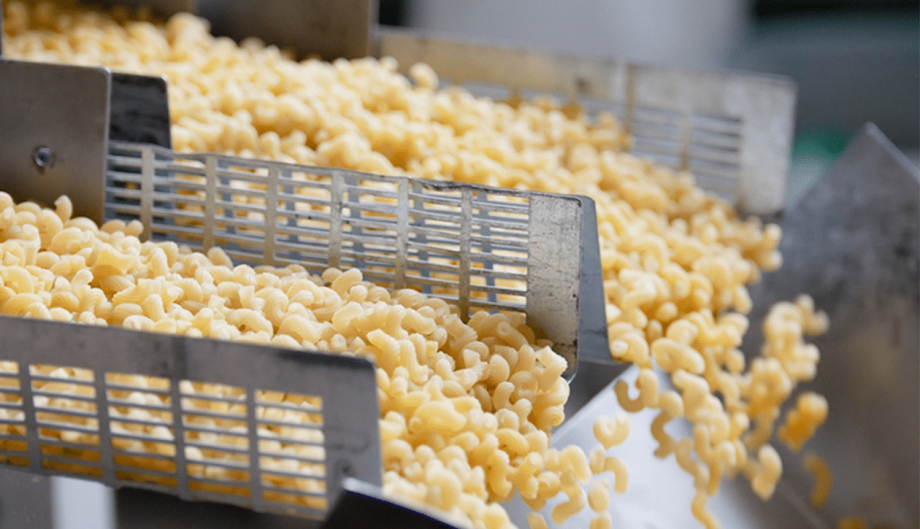
Revenue
Employees
At a glance
Challenge
Managing a project that includes refurbishing a warehouse, onboarding a new 3PL team, transitioning value-added services, and shifting 1.7MM cases of dynamic inventory while maintaining normal business operations
Result
Pariveda transitioned warehousing to new facilities before contractual deadlines, improving overall inventory efficiency and delivery performance.
IMPACT
The company improved inventory management and delivery metrics while extracting significant ongoing operational savings.
A $1.6B multinational food processing company employs over 3,000 people and produces private-label consumer packaged goods (CPG) in meal preparation segments.
FoodCorp* was divested from its parent organization, compelling a separation of the operational capabilities across the supply chain, including manufacturing and warehousing facilities, procurement, transportation, and other logistics.
The Challenge
Corporate divestiture required realignment of the organizations’ manufacturing and warehousing facilities.
Canada warehouse operations were strained prior to the divestiture, and separating the two companies’ activities was critical to restoring operational stability for both firms. FoodCorp enlisted Pariveda to manage the transition of their Canadian supply chain to an optimized footprint. The Pariveda team partnered with key stakeholders to plan and execute the remediation and preparation of a new facility, equipment acquisition and installation, onboarding of 3PL and Value-Added Service partners, and a multi-phase inventory transition plan.
The Result
How Pariveda aligned multiple workstreams for project delivery success:
- Developed and managed an integrated workplan incorporating facilities, operations, transportation, manufacturing and VAS, customer/business partners, and service teams.
- Coordinated and collaborated with leadership, planning, and operational teams in both the parent and divested organizations and multiple third-party logistics partners.
- Led cross-functional subject matter expert teams to execute program tasks, resolve issues, and manage the change across multiple user groups.
The Impact
FoodCorp achieved a successful realignment of its manufacturing and warehousing facilities, resulting in enhanced inventory management and delivery metrics, alongside substantial ongoing operational savings.
*We value our client’s privacy, so we have altered their name. The outcomes we achieved with them are genuine.